
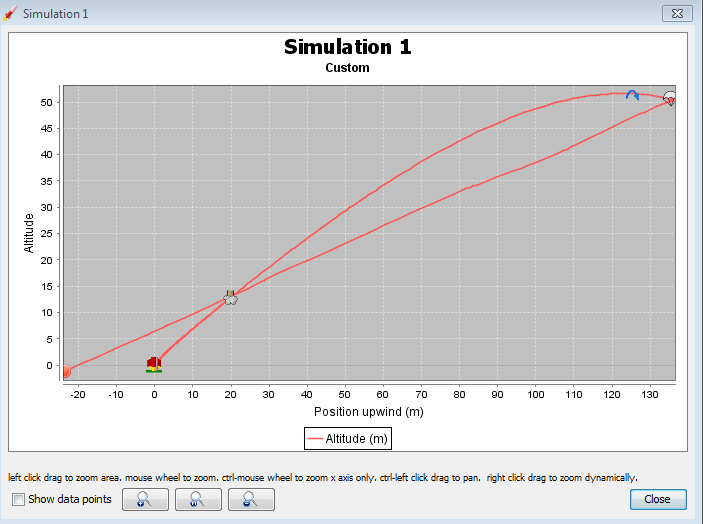
With SOLIDWORKS® Simulation solutions you can relax.
#Rocket simulation program software#
The third misconception is that simulation software results can’t be trusted. And, the more information you have about your designs, the more informed decisions you can make. Simulations don’t’ tell you necessarily whether your design is good or bad it helps you explore various options about your design so you can make informed decisions and reach the best possible option. So not only are you verifying your designs, but you’re also not over-engineering them. One of the most important simulation results you can see is if you are within your product factory and safety guidelines. The second misconception is that the software will only tell you if a design option is good or bad. We have developed our simulation software to help you replicate real-world conditions with the software so you can be confident and validate your designs like a pro. If you understand how your product works in the real world, then you can use simulation. After talking to hundreds of customers and thousands of users one thing is clear to me. Let me tell you why I believe that is false. The first misconception is that you need to have a PhD in engineering to use simulation software. Let’s look at some of the most common misconceptions. Today, I’m hoping to change your mind about that. I’ve been involved in the simulation industry almost two decades, and software has evolved but one thing that hasn’t changed are the misconceptions associated with simulation. Wrong! These days you don’t have to have a PhD or even be a specialist to use simulation. There’s a huge misconception that you have to be a specialist to use simulation software. If you’re up for that, then I want to challenge you to give simulation a try. A C++14 compiler (MSVC 2015 / g++5.0 / Clang 3.Many kick off the new year with resolutions, and for some, this includes trying new things.*If the user supplies advanced propellant internal ballistics parameters such as Prandtl number, adiabatic flame temperature, and gas viscosity (calculated using OpenBurn's internal CE solver), OpenBurn will calculate erosive burning effects on the grain surface.Ĭompiling OpenBurn has the following dependencies:.An internal chemical equilibrium solver for shifting or frozen equilibrium, so the user can easilyĬalculate necessary propellant constants such as C*, rho, gamma, T0, Pr, and more.A 2D geometric-based regression model allowing for any arbitrary 2D grain shape.Animated cross section view of the motor burn.
#Rocket simulation program skin#
OpenBurn will additionally calculate thrust and total impulse for the motor using the isentropic flow models, accounting for two-phase flow, skin friction, and divergent shape losses in the nozzle expansion cone.Grain regression and chamber pressure are calculated for a steady-state chamber based on Saint Robert's law r = aP^n.Motor cross section (grain geometry and nozzle) updates in real time as you design.OpenBurn is intuitive and easy to use for designing any solid rocket motor.OpenBurn is based on C++/Qt5, and has support across all major platforms (Windows, OSX, Linux). OpenBurn is an open-source solid rocket engine simulation and design platform designed from the ground up for the amateur
